Information about Packaging Barcode
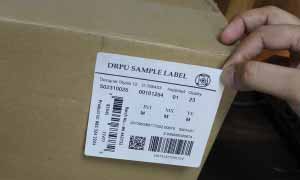
Packaging barcodes are a type of barcode used to track and manage products throughout the packaging and distribution process. They are typically used on various types of packaging, including boxes, bags, containers, bottles, and more. Packaging barcodes can be applied to primary packaging, which is the immediate packaging of a product, such as a bottle or box, or secondary packaging, which is the packaging used to group primary packages together, such as a case or carton.These barcodes can be scanned using barcode scanners or mobile devices to quickly and accurately identify the package and its contents.Packaging barcodes are barcodes that are applied to packaging materials, such as boxes, bags, and containers, to provide a unique identifier for each individual package.
Posted By: Techsavvy
Updated On: 14/April/2023
Purpose of Barcode in Packaging Industry:
In the packaging industry, packaging barcodes are used for a variety of purposes, including:
-
Inventory management:
Barcode labels can be used to track the location and movement of packages throughout the packaging and distribution process, helping to improve inventory management.
-
Quality control:
Barcode labels can be used to verify that the correct package has been filled with the correct contents, helping to ensure that product quality standards are met.
-
Traceability:
Barcodes can be used to track packages through the entire supply chain, from the point of manufacture to the point of delivery, enabling manufacturers to quickly identify and resolve issues that may arise.
-
Logistics:
Barcodes can be used to facilitate the movement of packages through the supply chain, allowing manufacturers to quickly and accurately track the movement of goods and ensure that they are delivered on time.
-
Marketing:
Barcodes can be used to create unique product identifiers that can be used in marketing campaigns, allowing manufacturers to track the effectiveness of their marketing efforts and make data-driven decisions about future campaigns.
Packaging barcodes can be applied to a wide range of packaging materials, including cardboard boxes, plastic bags, glass containers, and metal cans. The specific type of barcode used may depend on the material being labelled, as well as the scanning technology being used to read the barcodes. Common types of packaging barcodes include UPC codes, EAN codes, and QR codes.
Types of Packaging Barcodes
These barcodes can help to improve efficiency, accuracy, and traceability in the packaging and distribution process, as well as facilitate inventory management and product tracking throughout the supply chain.
-
⇛ Code 128:
A more versatile barcode type that can encode larger amounts of data and is often used in logistics and supply chain management.
-
⇛ GS1 Data Bar:
A newer barcode type that can encode more information in a smaller space, making it ideal for use on smaller packaging.
-
⇛ Code 39:
A widely used barcode type that can encode alphanumeric characters and is often used for industrial and logistics applications.
-
⇛ European Article Number(EAN):
Similar to the UPC, the EAN is commonly used in Europe and other countries.
-
⇛ Universal Product Code(UPC):
Used to identify consumer products in retail environments, such as grocery stores.
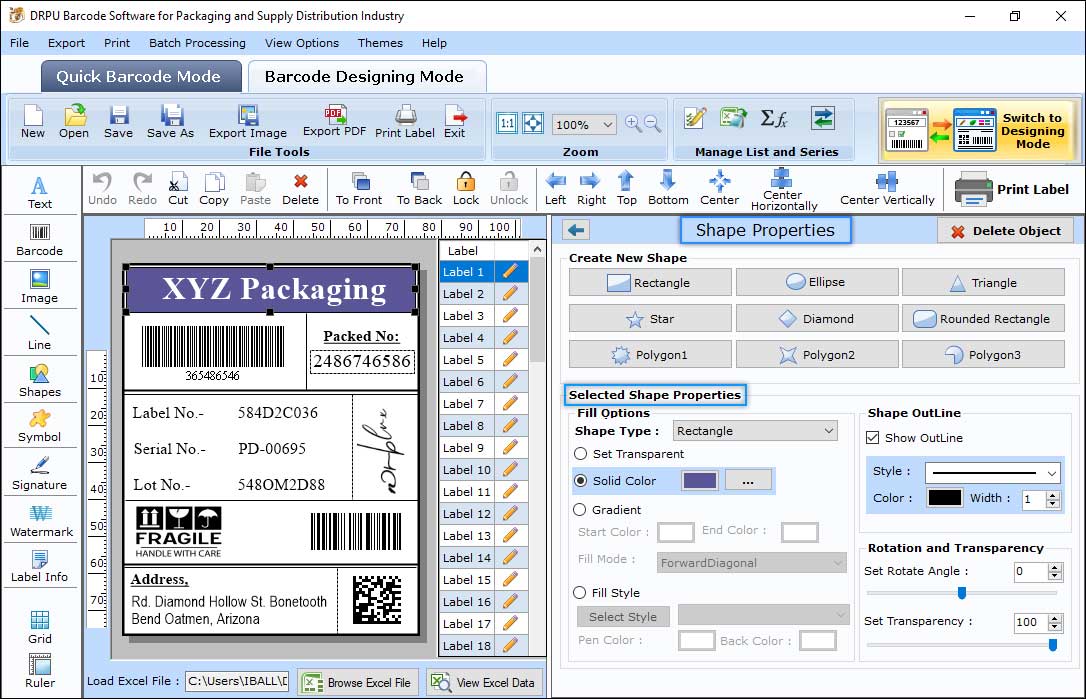
Benefits of using Automated Barcode Scanning System:
Automated barcode scanning systems can provide several benefits in packaging and shipping services, such as:
-
Increased Efficiency:
Barcode scanning systems can help to streamline the packaging process, reducing the time and effort required to label and track packages. This can lead to faster processing times, increased productivity, and reduced costs.
-
Improved Accuracy:
Barcode scanners can help to eliminate human error in the packaging process, reducing the risk of mislabelled or misrouted packages. This can improve customer satisfaction and reduce the cost of re-shipping or replacing lost packages.
-
Better Inventory Management:
Barcode scanning systems can help to track inventory levels in real-time, providing businesses with valuable insights into their inventory levels and enabling them to optimize their supply chain and prevent stock outs.
-
Enhanced Tracking and Visibility:
Barcode scanning systems can provide real-time tracking and visibility of packages as they move through the shipping process, allowing customers to track their packages and providing shippers with valuable data for optimizing their operations.
Overall, automated barcode scanning systems can improve the efficiency, accuracy, and visibility of packaging and shipping operations, leading to improved customer satisfaction, reduced costs, and increased profitability.
Regulatory Requirements for Packaging Barcode Systems:
The Regulatory Requirements for packaging barcode systems can vary depending on the country and region in which the products are being sold or distributed. In general, packaging barcode systems are used to identify products and facilitate their tracking and management throughout the supply chain. The use of barcode systems on packaging can help to improve efficiency, accuracy, and safety in the distribution of products.
The Regulatory Requirements for packaging barcode systems are typically set by industry organizations, such as GS1 and the Uniform Code Council (UCC), in consultation with governments and other stakeholders in the supply chain. These organizations have established standards for product identification and tracking, including the use of barcodes on packaging.
Other Countries and Regions may have their own regulatory requirements for packaging barcode systems. For example, in China, the China Food and Drug Administration (CFDA) has an established regulation for the use of barcode systems on pharmaceutical packaging. These regulations require that pharmaceutical products be labelled with a unique barcode that includes information such as the product name, manufacturer, and expiration date.
The Regulatory Requirements for packaging barcode systems are designed to ensure that products are tracked and managed efficiently, accurately, and safely throughout the supply chain. These standards are typically set by industry organizations, such as GS1 and the UCC, in consultation with governments and other stakeholders in the supply chain.
-
UNITED STATES
In the United States, the primary regulatory requirements for packaging barcode systems are set by the UCC, which is now known as GS1 US. The UCC is responsible for establishing standards for product identification and tracking, including the use of barcode systems on packaging. The UCC has established several barcode standards, including the Universal Product Code (UPC) and the Global Trade Item Number (GTIN).
-
EUROPE
In Europe, the primary regulatory requirements for packaging barcode systems are set by GS1 Europe, which is part of the global GS1 organization. GS1 Europe sets standards for product identification and tracking, including the use of barcode systems on packaging. The GS1 system is used in more than 150 countries around the world and is recognized as a global standard for product identification and tracking.