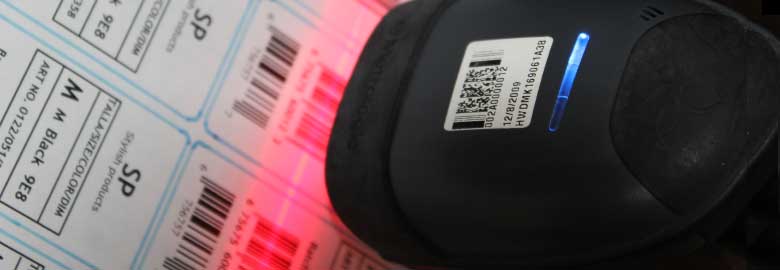
Benefits of using automated barcode scanning systems in courier companies
Automated barcode scanning systems can provide several benefits to courier companies, including:
-
Improved accuracy:
Barcode scanners can quickly and accurately scan barcodes on packages, reducing the likelihood of errors in tracking and delivery.
-
Faster processing times:
With automated barcode scanning, packages can be scanned and processed quickly, reducing the time needed to sort and load packages onto delivery vehicles.
-
Increased efficiency:
Automated systems can process a larger volume of packages in less time, enabling courier companies to handle more packages and customers.
-
Improved tracking and visibility:
Barcode scanning systems can provide real-time tracking information on packages, enabling customers to track the progress of their deliveries and reducing the likelihood of lost packages.
-
Enhanced customer satisfaction:
With improved tracking and delivery times, customers are more likely to be satisfied with courier services and more likely to use the service again in the future.
Overall, automated barcode scanning systems can help improve the efficiency and accuracy of courier services, leading to increased customer satisfaction and improved business performance.
Examples of Successful Courier Company Barcode System Implementations and its Benefits
-
FedEx:
FedEx implemented a barcode system in the 1980s to track packages and improve their delivery process. The barcode system allowed FedEx to track packages in real-time, reduce errors, and improve the speed of their delivery process. This resulted in improved customer satisfaction and increased market share.
-
UPS:
UPS implemented a barcode system in their sorting facilities to improve their package handling process. The barcode system allowed UPS to sort packages quickly and accurately, reducing errors and improving delivery times. This resulted in improved customer satisfaction and increased market share.
-
DHL:
DHL implemented a barcode system to track packages and improve their delivery process. The barcode system allowed DHL to track packages in real-time, reduce errors, and improve the speed of their delivery process. This resulted in improved customer satisfaction and increased market share.
-
USPS:
The United States Postal Service (USPS) implemented a barcode system to track packages and improve their delivery process. The barcode system allowed USPS to track packages in real-time, reduce errors, and improve the speed of their delivery process. This resulted in improved customer satisfaction and increased market share.
Overall, barcode systems provide numerous benefits for courier companies, including improved package tracking, reduced errors, and improved delivery times. These benefits result in improved customer satisfaction and increased market share.
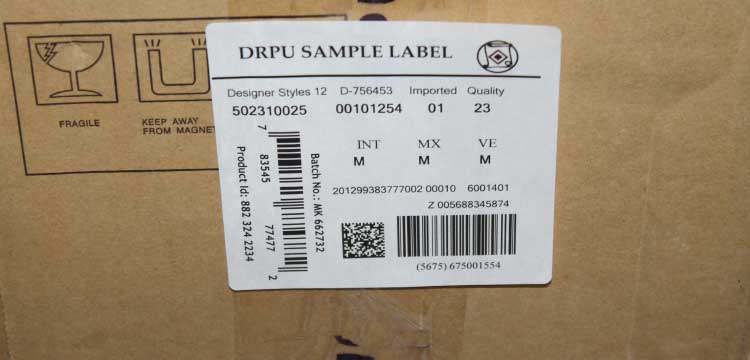
Challenges Associated with implementing barcode systems in courier companies
Implementing barcode systems in courier companies can provide several benefits such as improved package tracking, increased productivity, and reduced errors. However, there are some common challenges associated with implementing barcode systems in courier companies, which include:
-
Barcode Quality:
Poor barcode quality can lead to errors in scanning, which can affect package tracking. To address this issue, it is important to ensure that the barcodes are printed correctly and that the printer is well-maintained. It is also essential to use high-quality barcode scanners that can read barcodes even if they are damaged.
-
System Integration:
Barcode systems may need to be integrated with existing courier information systems such as order management or inventory management systems. To address this issue, it is important to ensure that the barcode system is compatible with the existing systems and that the integration is seamless.
-
Workflow Integration:
Barcode systems need to be integrated into courier workflows to be effective. To address this issue, it is important to ensure that the barcode system is designed to fit into courier workflows and that the staff is trained on how to use the system effectively.
-
Security:
Barcode systems can be vulnerable to security threats such as data breaches or unauthorized access. To address this issue, it is important to implement security measures such as authentication, encryption, and access control.
-
Cost:
Implementing barcode systems can be expensive, especially for small courier companies. To address this issue, it is important to evaluate the benefits and costs of the system and determine if it is cost-effective.
-
Environment:
Courier companies operate in different environments, and this can affect the quality of the barcodes. For example, exposure to sunlight or humidity can damage the barcodes. To address this issue, it is important to use barcode labels that are designed to withstand different environments.
In summary, implementing barcode systems in courier companies can provide several benefits but can also be challenging. Addressing these challenges requires a comprehensive approach that involves ensuring barcode quality, system integration, staff training, workflow integration, environment, security, and evaluating costs.
Best practices for selecting and implementing barcode systems in courier companies
Implementing barcode systems in courier companies can help improve package tracking and delivery accuracy. Here are some best practices for selecting and implementing barcode systems in courier companies:
-
Evaluate Your Needs:
Evaluate your courier company's specific needs and requirements, such as package tracking, delivery accuracy, and customer service.
-
Continuously Improve:
Continuously review and improve your barcode system and related processes to optimize your courier company's performance.
-
Choose Appropriate Equipment:
Choose appropriate barcode readers, printers, and software for the specific requirements of your courier company. Consider factors such as the type of packages being tracked, the size of your delivery network, and the speed of your delivery process.
-
Ensure Compatibility:
Ensure that the barcode system is compatible with your existing equipment and software, such as courier management systems or customer relationship management (CRM) systems.
-
Develop Standard Operating Procedures (SOPs):
Develop standard operating procedures (SOPs) for barcode system use, including how to scan barcodes, how to interpret barcode information, and how to troubleshoot common issues.
-
Integrate with Existing Systems:
Integrate the barcode system with your existing courier management and CRM systems to streamline your processes and reduce errors.
-
Ensure System Security:
Implement appropriate security measures to protect the barcode system from unauthorized access or tampering.
-
Monitor System Performance:
Monitor the system's performance regularly to ensure that it is functioning properly, and address any issues promptly.
In summary, selecting and implementing barcode systems in courier companies requires careful planning, evaluation, and training. The best practices for selecting and implementing barcode systems in courier companies include evaluating your needs, choosing appropriate equipment, ensuring compatibility, developing SOPs, training staff, integrating with existing systems, ensuring system security, testing the system, monitoring system performance, and continuously improving your processes.
Cost Implications of Implementing Courier Company Barcode Systems
Implementing a distribution barcode system can involve several costs, including:
-
Software costs:
This may include the cost of purchasing or licensing barcode software, as well as any other software needed to integrate the barcode system with other distribution systems.
-
Implementation costs:
This may include the cost of hiring IT staff or consultants to help design and implement the barcode system.
-
Training costs:
This may include the cost of training employees on how to use the new barcode system.
The benefits of implementing a distribution barcode system can include increased efficiency and accuracy in inventory management, order fulfillment, and shipment tracking. With a barcode system in place, distribution centers can quickly and easily scan items, reducing the likelihood of errors and saving time. The system can also provide real-time tracking information that can help optimize order fulfillment and shipping processes, reduce order cycle times, and improve supply chain visibility.