When black and white bars are smaller than the minimum size of 80%, bar and space width tolerances are reduced, making the printer's task more difficult and the symbols more likely to fail to scan. Variations in the printing or marking procedure, such as poor ink dispersion for printed codes or uneven surface pressure during the direct part marking process, can be a contributing factor in many reading difficulties.
Problems such as poor contrast and quiet zone breaches might occur when printing and marking equipment does not create and apply codes as planned. Other sources of poor barcode quality or irregularity might pose problems for barcode scanners that are set to "expect" symbols of a specific shape, skew, and uniformity.
Tips to Resolve Error:
- Create barcodes in the correct sizes so that the printer can easily print them.
- If your printer isn't printing the barcodes precisely, slow it down. Keep your printer clean and well-maintained at all times. Make sure the barcodes are appropriately aligned horizontally and vertically.
- Save barcode labels or tags in .EPS or .EMF format.
Barcode data that is incorrectly organised spells calamity. An incorrect check digit is one of the most common structural errors. A more difficult and common error is wrongly arranging the data sequence, or by mistake encoding an Application Identifier or application data such as "Expiration Date." Some, but not all, design software can help you avoid these mistakes.
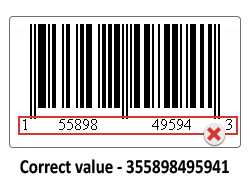
Tips to Resolve Error:
- Arrange the data in the barcode correctly. Always check out for the date and time you encoded in the barcode.
- Keep any graphics away from the middle and make sure the edges are visible.
- Always use check digits at the end of the barcode.
A legible barcode may return a no-read result in some instances due to the physical position of the barcode scanner relative to the code, not because of its print or mark quality. Barcode readers may have special criteria for reading codes at various focal distances, angles, or orientations, depending on the technology.
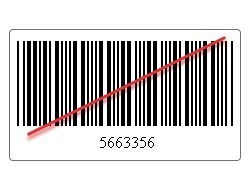
Tips to Resolve Error:
- When mounting a reader into equipment or presenting a code to a reader, it's critical to check the technical specifications to ensure that the constraints and needs surrounding the reader's position in respect to a code are taken into account.
- It may be necessary to use a barcode reader that is better adapted to supporting barcode distances, angles, and orientations that are unpredictable.
When a barcode is placed too close to a fold or edge of a package, the high reflectivity backdrop falls off too close to the leading or trailing edge of the barcode, causing a "virtual" quiet zone violation. This space separates the code from the surrounding marks, allowing the reader to "see" the complete code. The no print zone of 1D barcodes is located at the left and right ends of the barcode.
As a rule of thumb, the quiet zone should be at least 10 times the width of the 1D barcode's thinnest bar. The quiet zone is the space surrounding the complete symbol in 2D symbols. The Association for Automatic Identification and Mobility (AIM) mandates that each side of a 2D symbol must have at least one element (or cell) width.
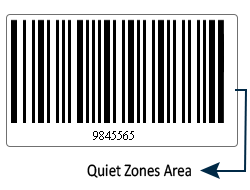
Tips to Resolve Error:
- To correct fundamental quiet zone infractions, just alter the printing or marking process – or the substrate – to fit the minimal quiet zone space requirements.
- Increase the width of the calm zone as much as possible to lessen the likelihood of reading errors.
The barcode is put on curves and corners, causing the picture to be distorted. On a strongly colourful product, a transparent, bar-coded container is utilised to reduce contrast. The package is reflective, causing "noise" that the scanner may detect. During delivery, the barcode is obscured by hazy or opaque plastic substance.
On most types of packaging, GS1 Standards dictate where the bar code should be placed. Consumer items should have barcodes on the natural bottom of the box or bag. ITF-14 barcodes should be placed on the sides of shipping containers for scanning by conveyor systems.
Tips to Resolve Error:
- If you wish to safeguard your shipping label during delivery, use clean plastic.
- Always use a level surface to stamp barcode labels.
- If the container or product packaging cannot be modified, redesign or reprint your barcode label and place it where it may be readily scanned.
Shape, contrast, element homogeneity, and substrate integrity are all examples of barcode distortion. Environmental changes can cause barcode labels to be distorted during the manufacturing process. Blotching ink is another factor that contributes to barcode distortion. No-read results might be caused by unintended material abrasions, markings, surface stains, or extra material (debris or even mounting fixtures).
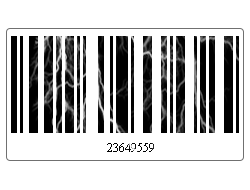
Tips to Resolve Error:
- Consistent barcode quality might be difficult to maintain once a barcode has been introduced into a production environment.
- The options for preventing or resolving barcode damage and distortion in operations that utilise barcodes to monitor and identify things even after they have been transferred between facilities or sold to consumers to be scanned by new barcode reading equipment are relatively restricted.
The width-to-height aspect ratio for each barcode symbology is defined by its own design specification. From every angle, the barcode should be straight forward to scan and read. When a barcode is truncated or shortened below the prescribed height, it becomes unreadable at any angle. A conveyor line's barcodes might be overlooked. Rescans are required for barcodes at checkouts.
Reduced bar width is an excellent approach to ensure that the printed barcode scans correctly. The most prevalent cause of barcode failure is incorrect bar width reduction (BWR). Measure the printed barcode width and height against the barcode in the design file to get the correct BWR.