Barcodes needed for your Packages and Labels
Barcodes used for packaging differ from other barcode systems in terms of the information they encode and their purpose. Packaging barcodes are typically used to track products throughout the supply chain, including inventory management, order fulfilment, and shipping. They may also include information such as expiration dates, lot numbers, and other product-specific data that is important for tracking and managing inventory.
Posted by: Techsavvy | Updated on:
Types of Packaging Barcode:-
There are several types of barcodes commonly used for packaging, including the Global Trade Item Number (GTIN), the International Standard Book Number (ISBN), and the Universal Product Code (UPC):
-
GTIN
The GTIN is a unique identifier used to track products throughout the supply chain. It is commonly used in the retail industry and includes a series of numbers that identify the manufacturer, product, and package size.
-
UPC
The UPC is a widely recognized barcode system used to identify products in retail stores. It includes a unique 12-digit number that identifies the product and is scanned at the point of sale to retrieve pricing and inventory information.
-
ISBN
The International Standard Book Number (ISBN) is a unique identifier used to track books and related products. It includes a series of numbers that identify the publisher, title, published date, and edition of the book.
In contrast, barcodes used in other industries, such as healthcare and logistics, may include additional information such as patient information, medication dosage, and shipping destination. These barcodes may also need to be more durable and resistant to environmental conditions to ensure accurate scanning throughout the product's life cycle.
Some Information about Packaging Barcode:-
Packaging Barcodes typically contain information such as the product's unique identifier, the manufacturer's information, and the batch or lot number. This information is used to facilitate the tracking and management of products as they move through the supply chain from the manufacturer to the retailer. packaging barcodes are an essential tool for manufacturers, distributors, and retailers to manage their supply chains and ensure that products are tracked and managed efficiently.
Manufacturers use packaging barcodes to manage their inventory and production processes. Distributors and retailers use packaging barcodes to track shipments, manage inventory levels, and facilitate sales transactions. When a barcode is scanned at the point of sale, the retailer can retrieve the product information from the barcode and use it to determine the price, manage inventory levels, and facilitate the sale.
The Unique Identifier encoded in the packaging barcode can be an EAN (European Article Number) or a UPC (Universal Product Code), which allows for easy identification of the product. The manufacturer's information encoded in the barcode can include the name, address, and contact details of the company. The batch or lot number can be used to track a specific production run of a product and can be used in the event of a product recall or to trace the source of a quality issue.
Download and Install Packaging Barcode Software
Overall, packaging barcodes are an essential tool for manufacturers, distributors, and retailers to manage their supply chains and ensure that products are tracked and managed efficiently.
Future of Barcode Technology in Packaging:-
The future of barcode technology in packaging looks promising, with continued advancements that will improve supply chain visibility, inventory management, waste reduction, safety, compliance, and customer experience. These innovations will help to make the packaging industry more efficient, sustainable, and customer-friendly.
The future of barcode technology in packaging is expected to see significant growth and development, with several advancements that will improve the packaging industry in several ways:
-
Improved supply chain visibility:
Barcode technology can be used to improve visibility and tracking of goods throughout the supply chain, from production to delivery. This will help to reduce inefficiencies and improve overall supply chain management.
-
Enhanced customer experience:
Barcode technology can be used to provide customers with real-time information about their orders, including tracking information, estimated delivery times, progress of the delivery, and other relevant information.
-
Enhanced inventory management:
Barcode technology can be used to improve inventory management in the packaging industry, reducing the chances of stockouts, missing stocks, and overstocking.
-
Reduced waste and errors:
Barcode technology can help reduce waste and errors in the packaging industry, by ensuring that the right products are delivered to the right locations at the right time.
-
Improved safety and compliance:
Barcode technology can help improve safety and compliance in the packaging industry, by ensuring that products are labeled correctly and that safety guidelines are followed.
Best Practices for Implementing Barcode Systems in Packaging
Selecting and implementing barcode systems in packaging requires careful planning and evaluation to ensure a successful implementation. Here are some best practices for selecting and implementing barcode systems in packaging:
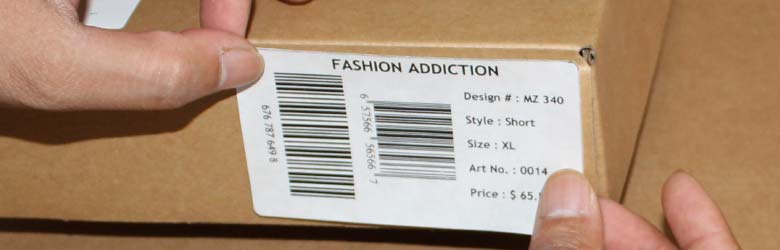
-
Identify Requirements
Identify the specific requirements for the packaging barcode system, such as the types of barcodes needed, the speed of the packaging process, and the integration with other several systems.
-
Research Available Options
Research the available options and select a system that has been designed for packaging applications. Look for a system that is compatible with your existing packaging equipment.
-
Ensure Compatibility
Ensure that the barcode system is compatible with your existing packaging equipment and software. This may involve choosing a barcode format that is accepted by your customers or clients.
-
Evaluate System Integration
Evaluate how the professional barcode system will integrate with your existing packaging technology infrastructure, such as conveyors, barcode scanners, and barcode printers.
-
Test the System
Before implementing the barcode system in packaging, test it in a controlled environment to ensure that it meets your specific requirements and is compatible with your existing systems.
-
Train Staff
Provide adequate training to staff on how to use the barcode system effectively, including how to scan barcodes, how to interpret barcode information, and how to troubleshoot common issues.
-
Monitor System Performance
Monitor the system's performance regularly to ensure that it is functioning properly, and address any issues promptly.
-
Conduct Audits
Regularly conduct audits help you to ensure that the barcode information matches the actual packaging label as well as the shipping information.
-
Establish Maintenance
Establish a proper maintenance schedule to ensure that the barcode system is regularly maintained and repaired as soon as required.
In summary, selecting and implementing barcode systems in packaging requires careful planning, evaluation, and training. The best practices for selecting and implementing barcode systems in packaging include identifying requirements, researching available options, ensuring compatibility, evaluating system integration, testing the system, training staff, developing SOPs, monitoring system performance, conducting audits, and establishing a maintenance schedule.